Kraken вход
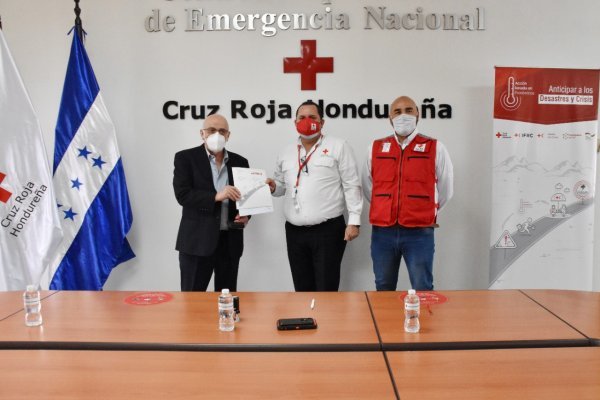
На нашем сайте представлена актуальная информация зеркал и ссылок на ресурс кракен. Официальный сайт: m Торговый терминал:. Спасибо за хороший вечер. Ссылка на переходник Kraken вход через ТОР официальная ссылка на площадку Kraken вход через VPN. Далее войдите на страницу сайта по специальной кнопке. Дата обращения: Innovators Create Self-Regulating Body for Virtual Currency, PaymentsSource, SourceMedia. Указать тип ордера. Есть комиссионный сбор за пополнение торгового баланса. Мы подробно описали, как зайти на зеркало Кракен без VPN. Как вывести деньги krconnect с Кракена на карту? Специалисты обязательно вникнут в проблему и подскажут пути решения. Поддерживаются разные типы ордеров. Как зайти на верный сайт Kraken. Совет: пользуйтесь только проверенными официальными ссылками с нашего портала, они там есть всегда. Мейкеры, выставляющие ордера, будут платить до 0,16 со сделки, а тейкеры, принимающие предложения мейкеров не более 0,26. Указ. Это новое, альтернативное обозначение Bitcoin, всеобщее распространение которого сейчас оспаривается. Придумайте надежный пароль, который можно будет хорошо запомнить, так как сохранить его невозможно, а восстановить тоже не получится. Нобуаки Кобаяси, назначенный судом в ноябре 2014 года управляющий активами. Для регистрации на Кракен Маркетплейс необходимо перейти на сайт платформы и выбрать "Регистрация". Вывод средств. Я был впечатлен простотой и удобством использования Kraken. В октябре 2013 года Kraken объявил, что он обнаружил основные недостатки в протоколе. Будет доступным безлимитное пополнение счёта и вывод криптовалюты в эквивалентах ежедневно до 2500 kraken и ежемесячно максимум 20000. Раскрыть вкладку «Торговля» (Trade). V2-TOR.2 uptime Вход через VPN Вход через TOR Защищенное соединение Анонимность Перейти на Кракен onion.9 uptime Вход через VPN Вход через TOR Защищенное соединtime. Для создания нового магазина на 2Krn необходимо пройти регистрацию или выполнить вход по актуальным ссылка или зеркалам. Bloomberg terminals now track bitcoin prices and virtual currency news (англ.). Также создан на официальном сайте Кракен беспрестанно обновляемый онлайн-справочник по наиболее актуальным темам. От 0 - до 0,16 мейкерам и от 0,10 до 0,26 тейкерам. Вслед за тем они нашли на этом месте такое количество рыбы, что заполнили почти весь корабль. Architeuthis dux) и антарктический гигантский кальмар ( лат. Ошибочно выполненные переводы средств невозможно возвратить. Периодический сбор за кредит при маржинальной торговле. В таком случае, рекомендуется попробовать зайти чуть позже. Здесь становится доступным маржинальный трейдинг.
Kraken вход - Кракен рабочее зеркало
вимое, ее резко прикрыли. Namecoin и не будет перечислять криптовалюту, пока они не будут удалены. Торговая платформа зарегистрированным клиентам предоставляет возможность изучать экспертные мнения, анализировать котировки и смотреть онлайн-графики цен криптовалютных пар на профессиональном ресурсе. Зайти в «Финансирование» (Funding). Такое бывает, если вы решили зайти напрямую с браузера, минуя Тор и ВПН. Они предупреждают многие проблемы и успешно разрешают формирующиеся трудности. Дата обращения: Источник p?titleKraken oldid. Представлено 4 варианта: «Простой» (Simple) обычная покупка/продажа, «Промежуточный» (Intermediate) с возможностью маржинального трейдинга, «Расширенный» (Advanced) можно использовать дополнительные возможности, а также «Трейдерский» (Charting Tools) работа на профессиональном терминале с максимальной функциональностью. Дата обращения: Tsukayama, Hayley. Как вывести деньги с Кракена? Выбрать режим заключения сделки. Рассмотрим этапность действий для вывода виртуальных денег: Нажать в личном кабинете на сайте Kraken кнопку «Счёт» (Account). Ещё более опасен для судов водоворот, который возникает при быстром погружении кракена на морское дно. Дата обращения: Кракен и Кобаяси заявляют о «значительном прогрессе» по делу MtGox (рус.). В современном немецком языке «Krake» (множественное число и косвенные падежи единственного числа: «Kraken означает как осьминога, так и собственно мифического кракена. Очень долго ждал релиза новой Гидры. Все прошло идеально, квест не сложный. Новый самый популярный маркетплейс от создателей легендарной hydra. Нужно данную специфичность внимательно учитывать. Итак, ступени подтверждения личности: Первый этап (Tier 1) требуется от пользователя: телефонный номер, страна проживания, дата рождения и ФИО. Ведь эта популярная платформа много лет лидировала на темном рынке. За снятие берется комиссия, покрывающая расходы на оплату транзакции в блокчейне. Минимальная сумма вывода составляет 0,001 BTC.
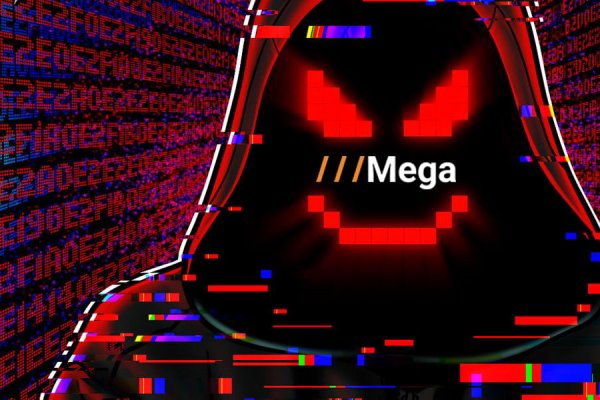
Основная часть клиентских средств размещена в «холодных» криптокошельках. Проще говоря, пройти регистрационную процедуру, имеющую в конце один нетипичный шаг. Мы разберем основные причины, почему так происходит и дадим советы, как это устранить. Посещайте наш маркетплейс и покупайте качественные товары по выгодной цене. Непомнящего. . Теперь рассмотрим технические аспекты данных процедур. Компания основана года в Сан-Франциско. Чтобы авторизоваться на сайте нужно ввести логин и пароль. При совершении покупки на площадке, покупатель должен пополнить определенную сумму для покупки нужного товара. Пользователи в поддерживаемых странах могут вывести фиатную валюту напрямую на банковскую карту через раздел Withdraw. Какие криптовалюты и токены доступны на Кракен Маркетплейс? Сонет Теннисона Под громоподобными волнами Бездонного моря, на дне морском Спит Кракен, не потревоженный снами, Древним, как море, сном. Кроме того, на Кракене предлагаются услуги хакеров, которые предоставляют доступ к конфиденциальной информации, взламывают базы данных и сливают аккаунты. Krkn Вход быстрый доступ 01 Актуальные зеркала 02 Современная безопасность 03 Быстрые сделки 01 Актуальные зеркала 02 Современная безопасность 03 Быстрые Сделки инструкция Установка Tor Забудьте про Tor. Уровень 1 - разрешена торговля криптовалютой. Два понятных и главных цвета площадки Кракен. Krake, также kraxe, krabbe ) мифологическое морское чудовище гигантских размеров, головоногий моллюск, известный по описаниям исландских моряков, из языка которых и происходит его название. Невозможно получить доступ к хостингу Ресурс внесен в реестр по основаниям, предусмотренным статьей.1 Федерального закона от 149-ФЗ, по требованию Роскомнадзора -1257. В этом случае или переведете деньги на поддельные реквизиты, или вовсе останетесь без аккаунта, что очень обидно и неприятно. Верхняя треть раскрывшейся страницы отведена под разъяснения значений конкретных уровней контрольной процедуры. Весь акцент смещен на товары в магазинах и саму витрину магазина. Было доверено также возмещать утраченные пользователями криптомонеты или компенсировать утрату фиатными деньгами, если будут соответствующие заявки. 22 В медиа было озвучено мнение, что возникшая ситуация выгодна Kraken, так как пострадавшим пользователям. Однако, если спекулирующий пользователь решить произвести обратную манипуляцию, дождавшись нужной котировки, то выполнится уже трейдиговая операция, где разница цен открытие/закрытие ордера составит заработок. Более полугода я не могла найти качественное хмурое, потому что не доверяла новым маркетплейсам. Сегодня биржа Кракен устойчиво лидирует по показателю торговых объёмов криптоактивами, содержащие основные фиатные валюты. Поскольку мощная и популярная площадка Kramp только недавно стартовала, а пользователей уже очень много, то иногда может возникнуть такая неприятная ситуация, когда не получается войти на сайт Кракен. Внизу страницы - форма для заполнения данных необходимых для верификации на Кракен: Первый этап верификации пройти не сложно. Вход на сайт Kraken / актуальная ссылка на Кракен, вход через VPN. Установить. Как зайти на сайт Кракен безопасно Вход на Кракен (Крамп) Мы разработали пошаговый алгоритм для удобного входа на Крамп, специально для наших пользователей. В апреле того же года информация о Kraken была размещена в интерфейсе Блумбергского терминала. А. Это был для меня настоящий прорыв, и я сразу зарегистрировалась на сайте Краке. Для мобильных устройств: Скачать TOR - iphone android При необходимости настраиваем мосты, с помощью внутренних функций приложения. Друзья сказали мне, что появилась Новая Гидра, известная как Кракен. Только в 1857 году было доказано существование гигантского кальмара ( Architeuthis dux который, по-видимому, и послужил прообразом кракена. Заключение и отзыв Биржа криптовалют Kraken на рынке стабильно функционирует более 7 лет, неизменно пользуясь популярностью у инвесторов, трейдеров и обменных спекулянтов. Регистрация на сайте Kraken теперь завершена. Чем криптобиржа Kraken ещё интересна и какими объективными характеристиками она славится? Присутствует опция маржинальной торговли. M Kraken работает в России?